Quick and Reliable Packaging Maker Repair Service Solutions to Lessen Downtime
In the affordable landscape of production, the performance of product packaging procedures pivots on the dependability of equipment. Quick and reliable fixing services are vital in mitigating downtime, which can lead to considerable financial losses and operational problems.
Significance of Timely Fixes
Timely repair work of product packaging devices are essential for preserving operational effectiveness and minimizing downtime. In the hectic environment of manufacturing and product packaging, also minor malfunctions can cause significant delays and efficiency losses. Attending to issues quickly makes sure that equipments operate at their optimal capacity, consequently securing the circulation of procedures.
In addition, routine and timely upkeep can prevent the acceleration of minor troubles into significant break downs, which frequently incur greater repair expenses and longer downtimes. An aggressive technique to maker fixing not just preserves the stability of the tools but likewise boosts the overall integrity of the manufacturing line.
Furthermore, timely fixings contribute to the durability of product packaging equipment. Machines that are serviced quickly are less likely to deal with too much deterioration, allowing organizations to optimize their financial investments. This is specifically essential in industries where high-speed product packaging is crucial, as the requirement for constant performance is extremely important.
Advantages of Reliable Provider
Reputable service carriers play a critical duty in making certain the smooth procedure of packaging makers. Their know-how not just boosts the efficiency of repair services but additionally contributes dramatically to the long life of equipment. Trusted company are geared up with the technological understanding and experience essential to detect issues precisely and execute reliable options promptly. This reduces the risk of repeating troubles and makes sure that devices run at optimum performance levels.
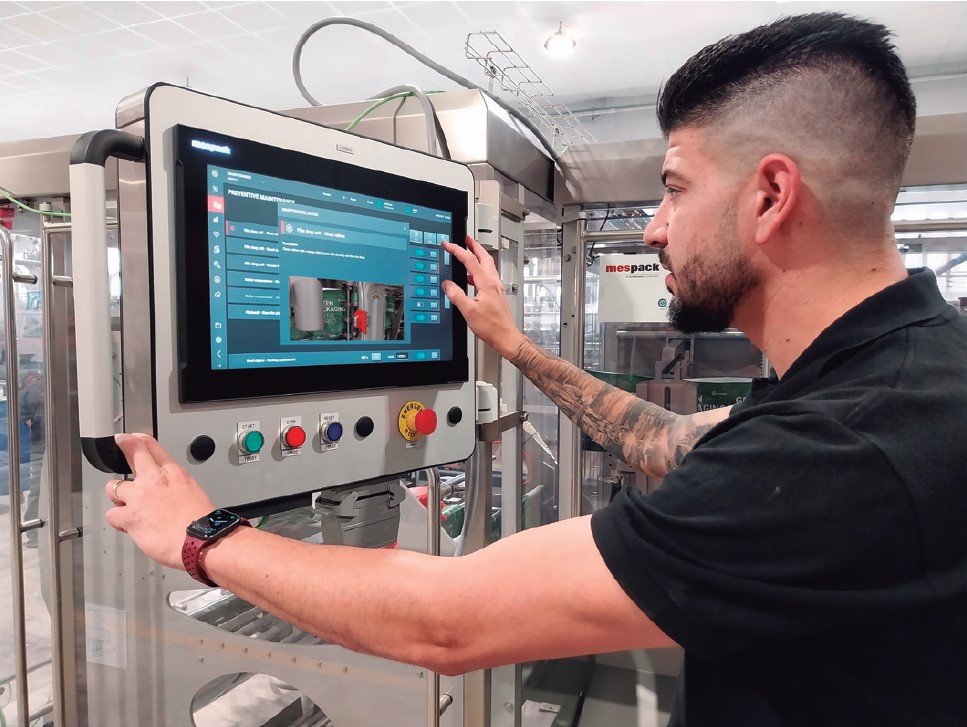
In addition, a trusted company provides detailed support, consisting of training and support for staff on device operation and maintenance best practices. This not just encourages staff members but also grows a society of security and effectiveness within the organization. Overall, the benefits of engaging dependable provider expand past instant repair work, positively impacting the whole functional workflow of packaging procedures.
Typical Product Packaging Equipment Problems
In the realm of product packaging operations, numerous concerns can endanger the effectiveness and functionality of equipments (packaging machine repair). Another typical concern is imbalance, which can trigger jams and irregular packaging, affecting item high quality and throughput.
Electric problems can additionally disrupt packaging procedures. Defective electrical wiring or malfunctioning sensing units may cause erratic device habits, triggering delays and raised operational expenses. In addition, software glitches can impede the maker's programs, leading to operational ineffectiveness.
Irregular item flow is another important problem. This can arise from variations in product weight, dimension, or form, which may impact the machine's capability to deal with products precisely. Insufficient training of operators can exacerbate these problems, as inexperienced personnel may not recognize early indicators of breakdown or might misuse the equipment.
Dealing with these typical packaging machine issues promptly is important to preserving efficiency and making sure a smooth operation. Regular inspections and aggressive upkeep can dramatically minimize these problems, promoting a trustworthy product packaging environment.
Tips for Minimizing Downtime
To minimize downtime in product packaging operations, executing a proactive upkeep method is important. Frequently scheduled upkeep checks can identify potential issues before they rise, making sure devices run effectively. Developing a regimen that consists of lubrication, calibration, and inspection of crucial parts can substantially reduce the regularity of unforeseen breakdowns.
Training team to operate equipment properly and identify early indication of breakdown can likewise play a vital function. Equipping operators with the understanding to perform fundamental troubleshooting can prevent minor concerns from causing significant hold-ups. Additionally, preserving a well-organized inventory of necessary spare parts can quicken repair work, as our website awaiting parts can result in extensive downtime.
Furthermore, recording machine performance and maintenance tasks can aid identify patterns and persistent troubles, permitting targeted interventions. Integrating sophisticated surveillance modern technologies can provide real-time data, enabling predictive upkeep and decreasing the risk of sudden failures.
Lastly, promoting open interaction in between drivers and upkeep groups makes certain that any kind of irregularities are promptly reported and dealt with. By taking these positive steps, services can improve operational effectiveness and substantially lower downtime in product packaging procedures.
Picking the Right Repair Service Solution
Picking the ideal repair work solution for packaging makers is a crucial choice that can substantially affect operational effectiveness. Begin by assessing the supplier's experience with your certain you can try this out kind of product packaging equipment.
Following, consider the provider's track record. Seeking feedback from various other businesses within your market can provide insights right into reliability and top quality. Accreditations and collaborations with acknowledged tools manufacturers can additionally indicate a dedication to excellence.
In addition, evaluate their action time and availability. A provider that can provide punctual assistance minimizes downtime and keeps manufacturing circulation steady. It's likewise critical to ask about service warranty and solution guarantees, which can show the self-confidence the copyright has in their work.
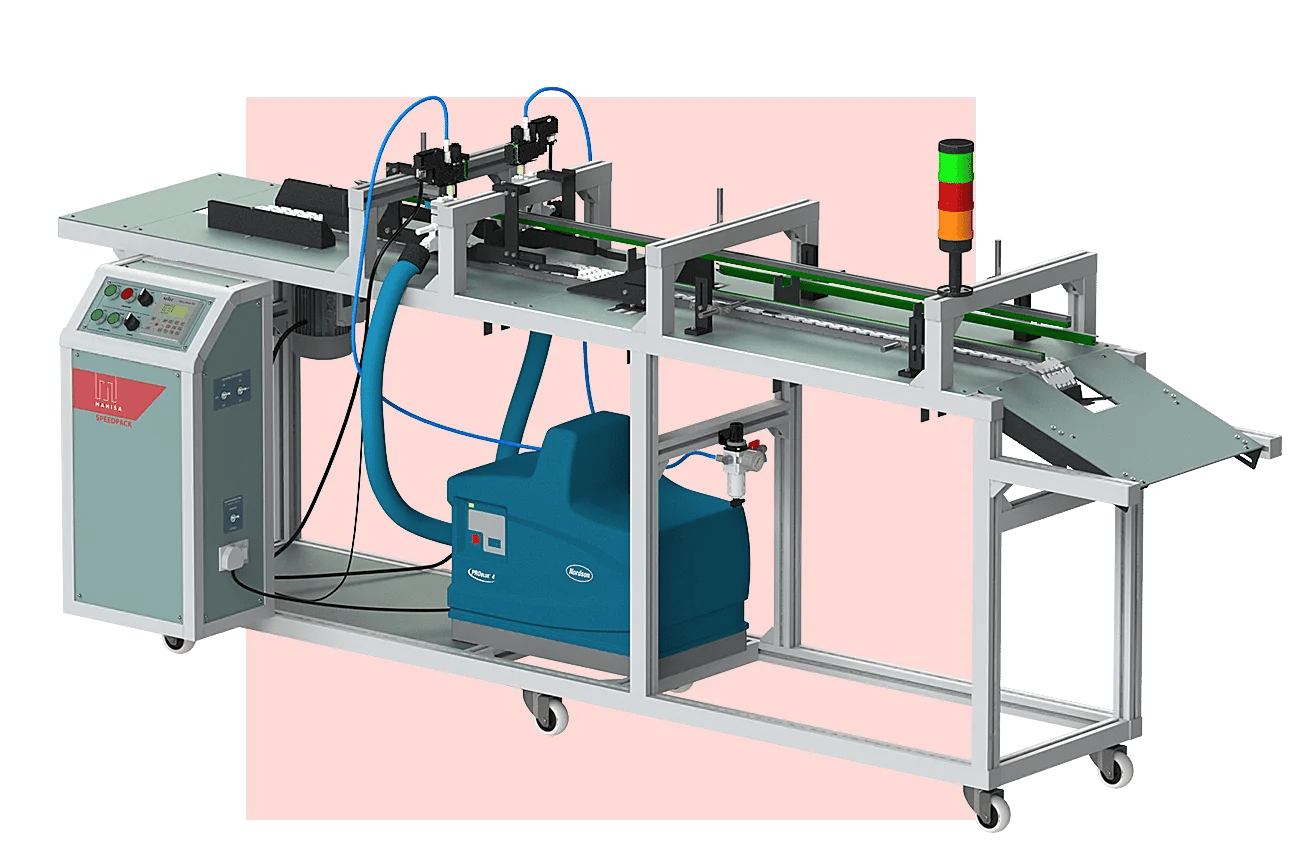
Conclusion
Finally, the value of reliable and fast product packaging machine fixing solutions can not be overstated, as they play a critical function in minimizing downtime and making certain operational performance. By prioritizing timely moved here repair services and selecting reputable provider, services can effectively preserve and address typical concerns efficiency. Applying proactive maintenance techniques and investing in personnel training more enhances the long life of packaging machinery. Eventually, a critical method to fix services promotes a much more resilient manufacturing setting.
Prompt fixings of packaging devices are crucial for preserving functional performance and reducing downtime.In addition, timely repair services add to the longevity of packaging machinery. In general, the benefits of engaging trustworthy service companies prolong beyond immediate repair work, positively impacting the entire functional operations of packaging processes.
